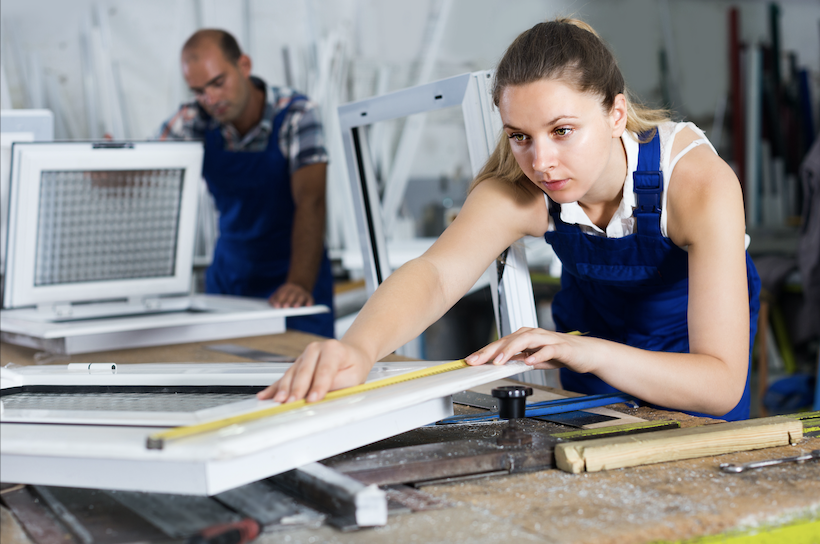
Polycarbonate or Acrylic Windshields
Should you use polycarbonate or acrylic windshields? Custom plastic windshields can benefit businesses in a variety of industries, from manufacturing facilities that use forklifts to agencies that require armored vehicles. They can be fabricated using a few different types of plastic materials. Two of the most common options include acrylic and polycarbonate. These materials provide great options for heavy equipment, motorcycles, and specialty glazing applications; however they do not meet federal regulations for standard automobiles.
Both of these materials offer plenty of benefits. So in order to choose the best option for your specific application and business needs, it’s important to look at the qualities of each one carefully. Here’s a rundown on these main options for custom windshields.
Benefits of plastic windshields
In general, plastics like acrylic and polycarbonate are perfect for custom and specialty windshields because of their light weight, durability, and ability to be formed into very specific shapes easily. More specifically, most plastics tend to weigh about 50 percent less than glass, which is beneficial both because it’s easier to install and because it puts less strain on the vehicle. The less weight it has to carry around, the more efficiently it’s able to travel. Since windshields and auto glass can take up a fair amount of the exterior, keeping that weight down can make a big difference over time. Ultimately, it may even lead to higher fuel efficiency and agility while reducing strain on the engine and other mechanical components.
Then there’s the durability factor. Plastics like acrylic and polycarbonate are significantly more impact resistant than glass. These materials are better equipped to absorb the impact from accidents or flying or falling debris. This means that when something hits a plastic windshield, the energy is spread out through the material and there’s less chance for it to completely break through or shatter. Even if the debris is able to break through, plastics are well suited to stick together and simply crack or warp, instead of getting completely broken apart. On the other hand, glass can easily shatter into harmful shards when exposed to any significant impact.
Finally, plastics can easily be fabricated into specific shapes, sizes, and forms. If you need a particular thickness for a windshield pane or want to replace a custom piece that isn’t readily available, working with a plastic fabricator gives you a convenient and economic solution.
Common applications
It’s not just basic vehicles that can benefit from windshields made using quality plastic materials. Companies in a wide array of industries have been able to take advantage of the added durability, ease, and convenience of custom plastic windshields. For example, those in the construction industry can use plastics for windshields in bulldozers and other types of heavy equipment. It can also be used in agriculture and forestry equipment, forklifts, recreational vehicles, golf carts, busses and other forms of public transportation. Additionally, the ability for certain plastics like polycarbonate to hold up against high impact also make them suitable for use in military and armored vehicles.
Benefits of acrylic
Custom acrylic windshields are known for offering exceptional visual clarity. They’re actually more clear than traditional glass, making the material perfect for applications where high visibility is a must. It’s also a very economical solution, generally costing less than glass and many other types of plastics, while still offering sufficient impact resistance, durability, and strength.
Acrylic is also known for being resistant to most scratches and visual imperfections. And if the material is scuffed up at all, it can easily be polished back to a smooth finish. It also doesn’t fade or yellow when exposed to UV rays. So it can be a popular option for vehicles that are stored outdoors or exposed to harsh weather conditions.
Benefits of polycarbonate
On the other hand, polycarbonate windshields are even more impact resistant than acrylic. While both are stronger in this area than traditional glass, polycarbonate is generally able to hold up better against high impact. There are even some bullet resistant grades available. This makes it the preferred choice in applications where vehicles may be exposed to rough conditions or ballistics, like military and armored vehicles.
It’s also durable against chips and cracks, and offers visual clarity that’s sufficient in most applications. Polycarbonate is generally easy to fabricate. It can be thermoformed or even bent and drilled without heating.
Both of these materials are polymers and come in a huge variety of sizes, thicknesses, and other varieties. So you can easily have a custom plastic windshield fabricated to meet your specific needs. Choosing the best option simply requires looking at the needs of your project and determining which plastic material best aligns with your specific goals.
If you’re looking into custom plastic windshields and want to explore either acrylic or polycarbonate, Polymershapes can help. We offer a wide array of customized plastic products that are well suited for windshields and other automotive and equipment related applications. Additionally, we provide fabrication services for companies throughout the Midwest and East Coast serving a variety of industries, including construction, machining, energy, and retail. Our Dayton fabrication center is ISO 9001 certified and ITAR compliant, and it is outfitted with state of the art equipment to give you the highest quality materials and fabrication capabilities possible. Our team can help you customize plastic materials for your specific size, safety, and strength requirements. To get started customizing windshields using acrylic or polycarbonate, visit our website to request a free quote. We’ll get back to you within 24 hours so you can get your next plastic fabrication project off the ground as quickly as possible.