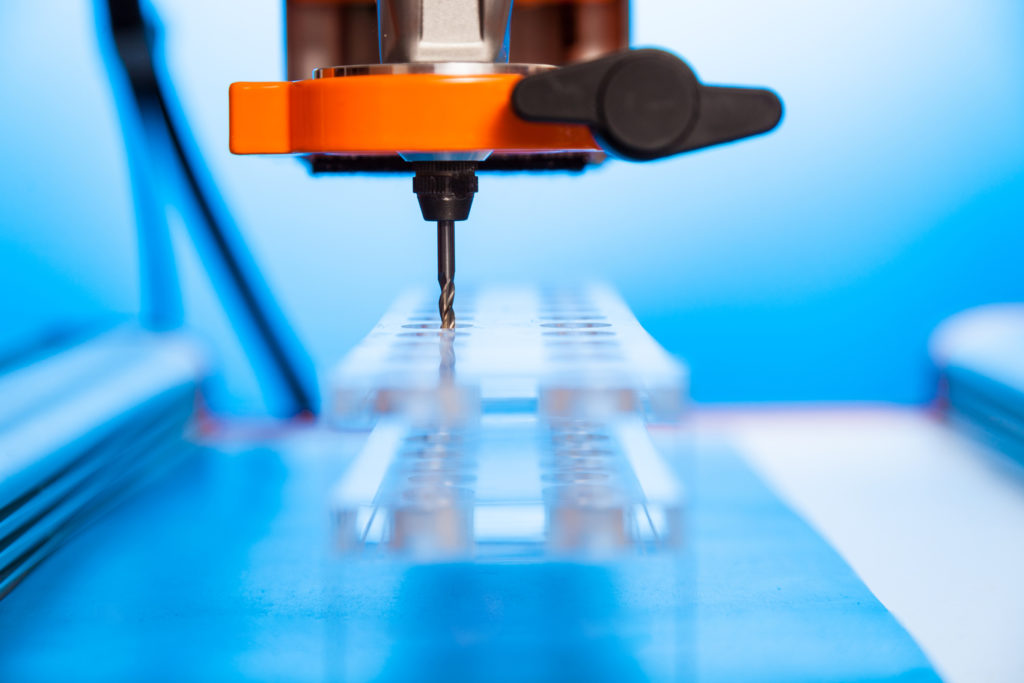
Acrylic plastic fabrication is one of the main services offered by Polymershapes. Acrylic is one of the most common and versatile plastic materials available. It’s transparent, strong, and lightweight, making it ideal for a long list of applications in various industries.
The chemical compound used to create acrylic is actually known as polymethyl methacrylate, which is a thermoplastic polymer. But it’s more commonly just called acrylic. Common brand names acrylic is also known by are OPTIX, by Plaskolite, plexiglass (or Plexiglas by Trinseo, formerly Arkema), or Acrylite by Roehm (formerly Evonik). If your company is considering acrylic for its plastic fabrication needs, here are some of the top things you need to know about this popular and versatile material.
Benefits of Acrylic
Some of the top benefits of acrylic include its visual clarity, light weight, strength, and resistance to heat and various chemicals. More specifically, acrylic offers clarity and light transmission comparable to glass. So basically, you can see clearly from one side to the other, almost as if there were no material there at all. This makes it ideally suited to applications where traditional glass may be used.
However, acrylic is significantly lighter than glass, which makes it easy to work with and install. It’s also perfect for use in precision components where bulkier materials may not fit, or in applications where mobility is an issue, since it’s easier to transport light materials.
Acrylic is also more impact resistant than glass. Since it is better suited to absorb energy from flying debris or impact, it is less likely to break or shatter when hit with a flying object. If any chips or small visual imperfections do occur, the surface can easily be polished to restore shine and optical clarity. Acrylic is also available in a variety of colors and finishes or textures.
Finally, acrylic is well suited for use in various environments. Acrylic is inherently resistant to UV, this makes it an incredibly durable and versatile material that can work even in outdoor applications or industrial venues.
Acrylic Plastic Fabrication – Methods and Processes
So how is acrylic actually fabricated to create these specific items that are so useful in an array of different applications? First of all, acrylic is formed using chemical reactions between compounds like methyl methacrylate, acetone, and sodium cyanide. Acrylic sheet may be formed via three methods: extruded, cast, or continuous cast. Once the acrylic sheet is formed, there are several different fabrication methods that can be used to customize and form it into specific shapes, sizes, and objects.
You can cut acrylic to desired sizes or flat shapes using methods including saw cut or routing, and then provide a clean edge with edge finishing, and polishing. With straight saw cuts, multiple acrylic sheets can be cut at the same time. CNC routing is used to cut curves, corners, and complete shapes out of acrylic.
Next, you have methods for bending and shaping acrylic. These include processes like heat bending. As the name suggests, heat bending involves applying high temperatures to the material so that it can be manipulated into specific angles easily.
There are additional customization methods available like drilling, acrylic welding, and general assembly. These are useful for those that need to work with multiple pieces of acrylic or various materials that need to be joined together within a single application.
If you’re interested in reaping the benefits of acrylic or learning more about the various plastic fabrication options available for your needs, contact Polymershapes. In addition to acrylic, we offer a wide array of plastic materials, along with fabrication and customization solutions to fit your specific needs. We work with clients throughout the Midwest and East Coast in a variety of industries, including automotive, construction, machining, energy, and retail. We’re also equipped to deliver quotes and products quickly, so you can always get the quality plastics you need for a variety of projects. To get started with your next acrylic fabrication project, visit our website to request a free quote. We’ll get back to you within 24 hours to help you get started.