Engineers and product specialists in the aerospace industry have very specific needs when it comes to the materials they use. This isn’t just true for the exterior; it also applies to all the aircraft interior components like bulkheads, panels, cockpit parts, structural components, and more which use aircraft interior plastics. Not only do the materials used in these applications need to meet stringent industry requirements, such as FAR 25.853 or OSU 6565, but they also need to have a niche set of qualities to be able to fit into much larger structures while supporting safe and efficient air travel.
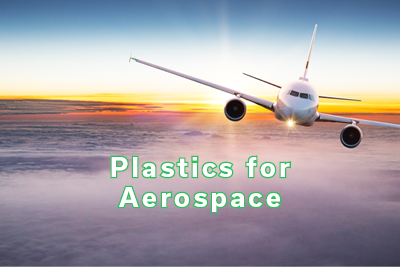
If you’re considering plastics for applications within the aerospace industry, here’s a basic guide to aircraft interior plastics.
Types of Aircraft Interior Plastics
Nearly every component in the interior of aerospace vessels can be made using performance plastic materials. Some examples of components that can be made using aircraft interior plastics include:
- Tray tables
- Bulkhead storage areas
- Luggage bins
- Seating parts
- Cargo containers
- Beverage carts
- Toilets
- Flooring
There are a huge variety of specific plastics available to fill all these needs. For example, PVC-acrylic, such as Boltaron, is often used in seating applications, such as food trays, seat backs, arm rests, and seat cladding, for its impact resistance and durability. Specialty grades of LEXAN polycarbonate and ULTEM are used in cabin areas, such as window trim, lavatories, or luggage compartments, to meet the toxicity requirements set forth by Boeing and Airbus. Additionally, plastics may also be used in structural components like beams and tubing that run throughout the aircraft.
Here are just some of the plastics that have applications within the aerospace industry:
- PVC-Acrylic
- PTFE
- Silicone
- PEI
- Nylon
- UHMW
- Polycarbonate
- ABS
- Acetal
These are just a few of the many materials that can suit a variety of needs in the aerospace industry. Reach out to your plastics supplier to find the options that work best for your specific needs.
Important Qualities of Plastics for the Aerospace Industry
Every material used in aerospace applications must meet stringent industry regulations and requirements related to flame-retardant qualities, chemical resistance, low toxicity, weight, and more.
More specifically, The Federal Aviation Administration requires that materials comply with a 12 or 60-second vertical burn FAR 25.853 requirement. . This test includes exposing materials to a two-gallon-per-hour oil burner, which is set to temperatures that one might find in a cabin fire. This test isn’t required for every single material used, but it is standard across many interior components used by major aerospace brands like AirBus, Boeing, and ASTM. The goal of these tests and certifications is to reduce the risk of cabin fires spreading quickly.
Another major reason why flame and heat resistance is so vital to aircraft interior components is to prevent large amounts of smoke and toxic gas from spreading throughout the cabin. Certain materials, when exposed to flame or extreme heat, emit toxic fumes, which can be especially problematic in enclosed spaces like airline cabins. So engineers and aerospace companies need to prioritize materials that meet the toxicity compliance standards of the industry, meaning they’re tested and proven not to emit toxic fumes when heated or burned. Many types of plastic are resistant to flames and are toxicity compliant as well. And there are additives that can easily be added to provide these qualities to aircraft interior plastics.
There are also several practical benefits of using plastics. Most notably, it’s significantly more lightweight than other materials like metal. Since there are so many aircraft interior components that must be in place during each flight, keeping the weight low on each one is what allows these structures to stay aerodynamic without sacrificing creature comforts on the inside. This also helps to reduce fuel consumption, which can save airlines and other aerospace operators significant money over time.
Then there are the engineering benefits. When designing aerospace equipment, the parts need to be very specific sizes and shapes in order to fit with the requirements and design of the larger structure. Since plastics are easy to fabricate using techniques like thermoforming, CNC routing, drilling, and machining, it’s possible to get components built to extremely specific industry standards and proprietary designs.
Finally, there’s the durability aspect. Aircraft interior plastics and structural components do not rust like metal. And they tend to last longer and require less maintenance than many other materials that could be used for crafting similar structures. This can save aerospace companies significant money on replacing parts and paying for team members or outside service providers to perform repairs and maintenance tasks on an ongoing basis. It also keeps select aircraft designs relevant for longer periods of time, meaning there’s less need to constantly redesign and produce brand new models after the interior parts have worn down. Basically, if a company’s goal is to procure top quality aerospace parts that serve their bottom line without sacrificing safety and efficiency, aircraft interior plastics offer seemingly endless benefits to the industry.
If you’re looking for a supplier for aircraft interior plastics, reach out to Polymershapes today. We offer a huge array of performance plastics that stand up to the rigorous testing standards of the aerospace industry, including those that are flame and toxicity compliant. Our team is well versed in the unique needs of the industries we serve, including aerospace, so they’re able to point clients to the specific materials, grades, and conversion services that best suit these requirements. Additionally, our local facilities are spread throughout the country and outfitted with top quality conversion and cutting equipment to customize every order to your exact specifications. If you’re ready to reap the benefits of quality aircraft interior plastics from Polymershapes, just visit our website to find your local branch and reach out to start your next order.