Plexiglass is a common name for acrylic plastic panels. Those in the plastics industry know the term well and likely have a firm grasp on the characteristics of this popular material. But even those who don’t deal with acrylic regularly likely have at least some familiarity with the term “plexiglass”, since it is so widely used across industries. However, you may not know all the attributes and applications that make plexiglass such a household name.
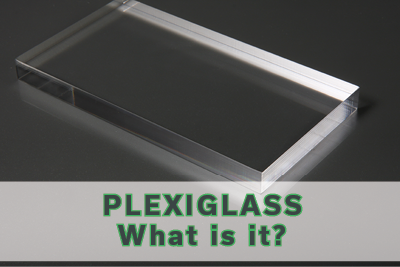
The now common term actually originated back in 1933 as a brand of clear-cast acrylic sheets known as “Plexiglas.” However, over time the brand became so synonymous with the material that the terms “plexiglass” and “acrylic” are basically used interchangeably today, just as Kleenex and Oreos have become synonymous with tissues and sandwich cookies. So you may hear something called “plexiglass” that isn’t actually from the brand that created “Plexiglas” back in the 1930s.
So what is plexiglass exactly? The petroleum-based thermoplastic material is naturally clear and lightweight. It is often manufactured in sheets and can serve as a replacement for glass in many instances. It is up to ten times more shatterproof than glass, so it is often preferred in applications where impact resistance is necessary. Here’s a closer look at some of the most powerful benefits and attributes of plexiglass.
Benefits and Attributes
One of the most notable qualities that draws companies to plexiglass is its strength and impact resistance. Acrylic panels can be up to ten times more shatterproof than traditional glass, depending on their thickness. Since the material is more flexible and less dense, it is better equipped to absorb the energy from impact instead of immediately shattering when struck, as glass is likely to do. Even if acrylic does break under extreme pressure, it generally just separates into large dull pieces, so it’s not nearly the safety hazard that shattered or broken glass can be.
Durability is another important attribute for many users. This is about more than just impact resistance; acrylic can also stand up against tension or pressure since it is slightly flexible. The surface can scratch when exposed to sharp or abrasive objects, but it can also be polished. So certain types of damage can be buffed away and the original surface may be restored.
Acrylic plastic is also incredibly lightweight since the polymer is not as dense as glass or many other plastic materials. This makes it incredibly easy to transport and handle. It can even make certain processes more efficient if used in machinery with moving parts, since the motor or engine may not have to work as hard as it would when moving heavy or bulky materials.
Though acrylic can be made in a wide array of colors and finishes, plexiglass is most often associated with clear, flat panels. In these applications, the material offers excellent optical clarity. So it’s ideal for applications where it’s important to have the ability to see through to the other side.
However, it is also easy to customize acrylic plastic in a variety of ways. More specifically, it can be cut to size, produced in various thicknesses and gauges, and even have different finishes added like matte, glossy, or different colors. Since it’s a thermoplastic, it can even be formed into various shapes when exposed to enough heat. So even though plexiglass is most often associated with flat, clear panes that look like glass, the actual material is much more versatile, allowing it to be used for a much wider array of applications.
Industrial and Commercial Applications for Plexiglass
Plexiglass has applications in a wide array of industries, including construction, transportation, and retail. Though these are far from the only potential uses for acrylic plastic, here’s a deeper look at some of the most common industrial and commercial applications for plexiglass.
In the construction industry, plexiglass is often used as a replacement for glass. It can be used in nearly any application where glass panes can be used, but where it would be useful to have a more lightweight or impact-resistant material. For example, it is often used in cabinet fronts, siding and roofing for greenhouses, and skylights.
In the transportation industry, acrylic is especially useful because of its durability, optical clarity, and low weight. It still allows operators to clearly see around their vehicles while providing sufficient protection. And the low weight allows vehicles to maintain optimal fuel efficiency since the engine doesn’t need to work as hard to carry around extra bulky components. Specifically, plexiglass is often used in operator protection panels in busses or public transport vehicles, as well as interior components like bulkheads.
For retail businesses, acrylic can be used in nearly any type of signage or display. Clear panels can be used in point-of-purchase cases, allowing in-demand products to be easily visible and protected from potential theft or damage. The material is also durable enough to work in outdoor signs and storefront windows. It can even be formed and cut to create custom shapes like letters. And since it’s so lightweight, it can easily be transported to different locations, an ideal quality for businesses that attend trade shows or need to display their products at fairs or special events.
If you’re ready to reap the many benefits of plexiglass for your own applications, your local Polymershapes facility can help. We carry acrylic sheets and a variety of other high-performance plastics from top manufacturers. And our local facilities can customize materials to your exact specifications. Visit our website to find your local branch and reach out for a quote.